Water Based Urethane Gloss
$50.00 – $159.00
- Tenacious adhesion to concrete floors
- Low VOC, water based formula
- Excellent gloss properties
- Superior resistance to common chemicals, solvents, and hot tire pick-up
- Description
- Dry Times
- Data
- How to Use
- Video
- Urethane Gloss FAQS
This Water Based Urethane Gloss is a high solids, two-component aliphatic polyurethane. To begin with, it is a high-performance material. Due to this, it has excellent hardness, abrasion resistance, hot tire resistance, and chemical resistance. Additionally, it has a low VOC, as well as, a low odor system with multiple uses. This makes the water based urethane perfect for interior floors surfaces. The product is an excellent gloss urethane and has tenacious adhesion. Thus, it is applied to concrete surfaces easily. This urethane gloss is great for prep and seal projects, especially on stained concrete floors, or over partial flake epoxy systems.
Advantages to CFS – Water Based Urethane Gloss:
- Excellent abrasion and wear for longer use
- Won’t yellow, UV resistance
- Hot tire, chemical, and abrasion resistance
- Low odor makes it great for indoor work
Pot Life | 45-60 Minutes |
Recoat or topcoats | 6-12 Hours |
Light Foot Traffic | 16-20 Hours |
Full Cure; Heavy Traffic | 4-7 days | based on 70 degrees, 50%RH. Temp. greatly effects curing. |
SURFACE PREPARATION: The concrete surface must be deemed mechanically and structurally sound, thoroughly clean of debris and completely dry. Concrete must be
fully cured a minimum of 28 days. It is recommended to prepare the concrete surface by mechanical means such as shot blasting or diamond grinding with 30 grit or coarser
diamonds to achieve a CSP-2 to CSP-3 profile. If using in a thin mil system such as acid stain, dye & seal, 2 or less clear coats, etc., an 80 grit diamond may be acceptable
to minimizes visual scratches in the finish, or the use of our 30 grit Concrete DNA Satellite pad. Vacuum concrete surface several times until dust thoroughly removed. If
applying over an existing, fully bonded coating that is outside its recommended recoat window, the surface should be sanded thoroughly with a 60-120 grit sanding screen
until the surface is completely dulled with scratches. Vacuum dust thoroughly, rinse with clean water and remove excess water with a wet/dry vacuum or floor scrubber.
Allow surface to dry completely prior to application of coating. Where applicable and with adequate ventilation, wipe the surface with acetone and a microfiber dust mop.
CAUTION: Acetone is extremely flammable! If using acetone follow all safety precautions, make sure no pilot lights, open flames, sources of static electricity, sparks or
extreme heat sources are present. Use recommended personal protection for acetone.
If mechanical floor grinding means of preparation are not suitable, it is recommended to prepare the surface with Super Blue and a 30 grit Concrete DNA Satellite pad. This
preparation method is only suitable for completely un-sealed, bare concrete surfaces. Apply Super Blue solution evenly on the surface using brushes, mops, brooms or an
approved floor scrubber and keep wet on the surface of 10 – 15 minutes. Remove excess acid solution with a wet/dry vacuum of floor scrubber. Rinse surface thoroughly with
clean water and on the final rinse use EZ Clean to neutralize the surface pH. Inspect the floor to ensure the surface has reached an even and adequate surface profile. Repeat
the acid etch and neutralizing steps as necessary to achieve correct profile. Allow the floor to dry thoroughly for 24-72 hours prior to applying this product. ALWAYS use
proper personal protective equipment when working with muriatic acid.
Substrate, air and material temperatures must be no less than 50°F and not exceed 80°F. If applied outside these limits the coating may not achieve adequate film formation
and may have excessive air entrapment, bubbles, blushing or hazing. Please note that higher substrate, air and material temperatures as well as excessive humidity may speed
the cure rate of this product. Cooler temperatures and lower humidity may slow the cure rate of this product.
FOR PERSONAL PROTECTION USE GLOVES, GOGGLES, RESPIRATOR AND OTHER NECESSARY PPE. REFER TO SDS PRIOR TO USE!
TINTING: Tint with Water Based Color Pigment. 32 oz. per 2.5 gallons is suggested for a solid, opaque finish. Always add color to Part A and drill mix for 2-3 minutes prior to
blending A and B. Color may settle during long term storage and be difficult to redistribute. Always test for color acceptance prior to full application. Multiple coats may be
necessary for total opacity. Refer to physical color chart for color selection.
MIXING: If mixing less than a full kit, mix Part A and Part B separately with a stir stick, low speed mixer or vigorously shake containers prior to measuring out the smaller kit
to ensure uniform distribution of all ingredients. In a clean mixing container, blend 4 Parts A and 1 Part B using a drill mixer for 2-3 minutes. Avoid creating a vortex in the
material which could introduce air and/or moisture content to the mixture. Do not mix more than can be applied within the usable pot life time frame. DO NOT THIN!
POT LIFE: This product has a potlife of approximately 45 minutes.
APPLICATION: Using a brush and/or 3/8” nap shedless roller, dip and roll the mixed material from a roller pan. 18” rollers are recommended for any surface to speed up
application time and reduce roller marks. Start by placing the wet roller at one corner of an approximate 4’ x 4‘ square and roll the material at an angle to opposite corner
applying no pressure to the roller. Spread the material across only that square and immediately back-roll to even out material and roller lines. Adjust the size of your square
as needed based on the amount of material being applied with the roller. After finishing the square, move on to the next square using the same technique. On seamless floors (no saw cuts) or bigger floors this products works well by pouring on the floor and evenly spreading with an 18″ 3/8″ nap roller and achieving an “even milk” appearance. Do not over roll. While applying
keep a wet edge to prevent roller marks. It is recommended to work in sections usually using control joints as dividers to ensure proper application results. Apply the mixed
material within the usable pot life time frame. If the material becomes thick while applying and sticking to the roller, stop applying and discard the mixed material. At this
point it has reached the end of the usable pot life. Do not allow to puddle! Use a brush to remove excess coating in joints.
RECOATING: If possible, recoat within the suggested recoat window located on page 1. Apply additional coats in the same manner as the first coat. Note that higher
substrate, air and material temperatures as well as excessive humidity may greatly reduce the acceptable recoat window of this product. When working in higher
temperatures, always recoat as early in the recoat window as possible to avoid failure between coats. If recoating outside the suggested recoat window (see page 1) or
beyond 24 hours, sand using a 80-220 grit sanding screen to ensure adequate adhesion between coats. Vacuum dust thoroughly, rinse with clean water and remove excess
water with a wet/dry vacuum or floor scrubber. Use a ‘water rinse’ when necessary. Allow surface to dry completely prior to application of coating. Where applicable
and with adequate ventilation, wipe the surface with acetone and a microfiber dust mop. CAUTION: Acetone is extremely flammable! If using acetone follow all safety
precautions, make sure no pilot lights, open flames, sources of static electricity, sparks or extreme heat sources are present. Use recommended personal protection for
acetone.
PLEASE NOTE: Applying material outside the suggested parameters may result in product failure. It is always recommended to test the product in a small, inconspicuous area
(on the same concrete substrate) for desired results prior to application. Coverage rates may vary for all coatings and substrates depending on porosity, density, texture etc.
When applying, adhere to suggested coverage rates. Applying too thin of a coating may cause inadequate film formation, limited performance expectations and/or undesirable
finish. Applying too thick may result to bubbling, hazing, etc. DO NOT USE ON BRICK.
COF WARNING: OSHA and the American Disabilities Act (ADA) have now set enforceable standards for slip-resistance on pedestrian surfaces. The current coefficient of
friction required by ADA is .6 on level surfaces and .8 on ramps. Concrete Floor Supply recommends the use of slip-resistant aggregate in all coatings or flooring systems that
may be exposed to wet, oily or greasy conditions. It is the contractor and end users’ responsibility to provide a flooring system that meets current safety standards. Concrete
Floor Supply nor its sales agents will be responsible for injury incurred in a slip and fall accident. For interior floors subjected only to foot traffic, Cherry Glo may be used as
an acceptable slip-resistant coating as it meets requirements for ASTM D2047.
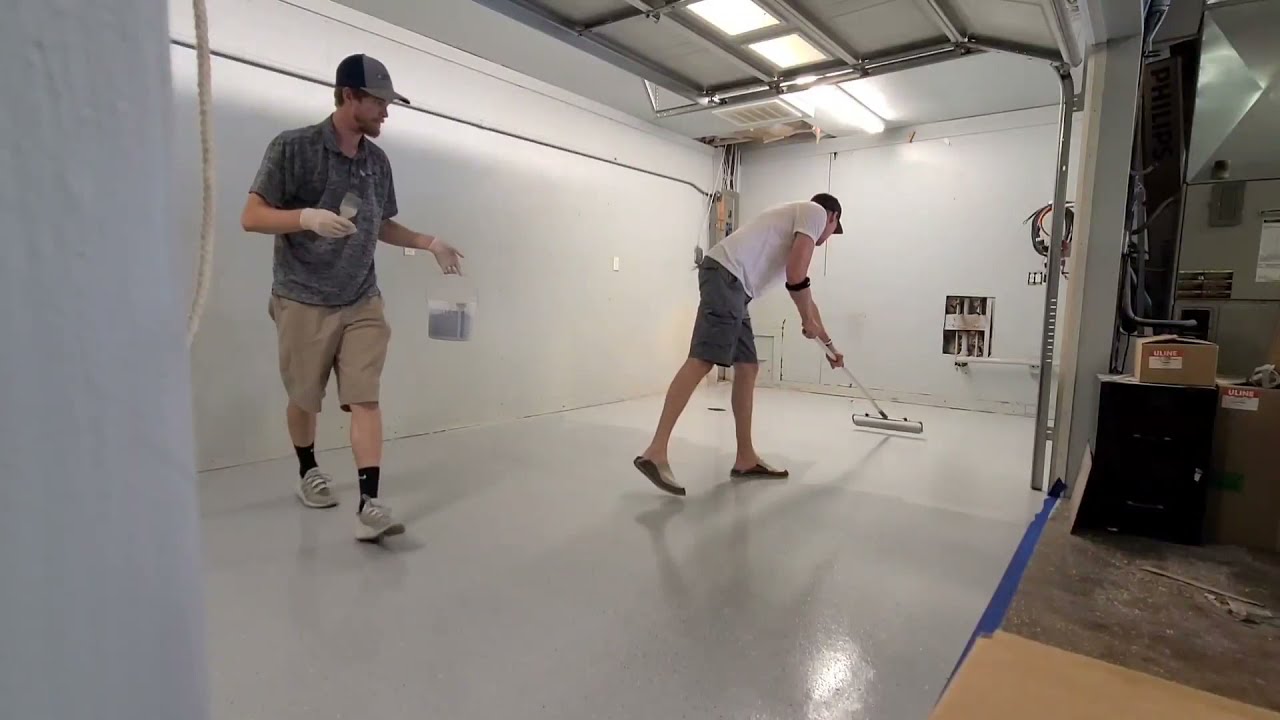
Question: Can you broadcast flakes into WB Urethane Gloss?
Answer: Yes, WB Urethane Gloss can accept partial broadcasts of flakes. We have pigment packs so you can pigment your base-coat of WB Urethane, broadcast your flake, then clear coat with WB Urethane (unpigmented). This system has extremely high bond strength and durability and will outperform the big box store stuff by a long shot.
Question: How long will Urethane Gloss hang out in the bucket?
Answer: This product will last in the bucket for up to 45 min.
Question: What is the best product to go over an existing Rustoleum garage epoxy?
Answer: First, you’re only as good as what you go on top of so keep that in mind. Compromised floors should be ground and removed. From what we hear on a daily basis you would be best to never put down a big box store floor coating(like Rustoleum) at all, but if you have one down and you just want to “go over it” our WB Urethane Gloss is a great option. This product can be pigmented gray or left clear. Our WB Gloss Urethane has unbelievable adhesion. We would recommend a good cleaning prior and a dry sand screen with around a 100 or higher grit screen prior to coating.
Question: What is the best top coat for a metallic floor?
Answer: Our urethane Gloss/Matte is the most common top-coat for a metallic epoxy floor coating. With great durability and adhesion, this product does very well as a top coat.
Question: Can Urethane Gloss be applied over radiant heat?
Answer: Yes, it is very common with shop style homes where they want a “concrete look” and have radiant heat. (Don’t have the system on during install or curing) Our Water Based Clear system which features Urethane Gloss is one of the most popular systems for that. You Don’t have to apply this product clear, it can also be pigmented as well.